4차 산업과 디지털 트윈
Industry 4.0 (4차 산업):
2016년 1월 20일 스위스 다보스에서 열린 세계경제포럼에서 언급되기 시작했으며, 3차 산업혁명을 기반으로 한 디지털과 바이오산업, 물리학 등의 경제를 융합하는 기술혁명으로 기계 학습과 인공지능으로 자동화와 연결성이 극대화되는 산업 환경의 변화를 의미합니다.
Digital Twin (디지털 트윈):
4차 산업 혁명이 가져올 신기술 중 한 가지입니다. 디지털 트윈은 산업 기기나 공장 등의 물리적인 세계를 컴퓨터에 재현하는 것을 가리킵니다. 제품의 모양뿐 아니라 기기나 공장에 지금 무슨 일이 일어나고 있는가 하는 실시간 정보를 복사하는 것입니다. 디지털 트윈이 있으면 어떤 부품이 어느 정도까지 소모되어 있는지를 해석해서 교환할 필요가 있는지 등을 고장이
발생하기 전에 판단하기 쉽습니다. 공장에서 가동되고 있는 장치를 멈추지 않고 가동 조건을 바꿀 경우에는
어떤 영향이 발생하는지를 검증할 수도 있습니다. 기기나 공장의 가장 적합한 운용 방법을 추구할 수 있고
가동률 향상에도 도움이 됩니다. (‘세상을 바꿀 테크놀로지 100’, 닛케이
BP)
- 다음 산업혁명에서 생존하기 위한 기계 설계에 대한 시스템 접근 방식 채택 -
1. 차세대 산업 혁명: Cyber-Physical 시스템으로서의 기계
자동차 산업은 큰 변화를 겪고 있습니다. 고급 계산 및 통신 기술은 기계 제조업체들이 제품을 설계하는 방식에 있어 획기적인 변화를 가져올 만큼 상당한 수준에 도달했습니다.
주요 제조업체들이 전용 메커니즘에서 메커트로닉스 또는 Cyber-physical 시스템으로 전환했다는
것은 제조업체들과 고객이 더 이상 기계 설계로 인해 제약받지 않는다는 것을 의미합니다. 그 대신, 서보 액추에이터 메커니즘의 동작을 정의한 기계와
제어 소프트웨어는 유연한 제조, 처리량, 에너지 관리 및 기계 수명 가치를 위한 상당한
기회를 제공합니다.
결과적으로 오늘날 비용 절감 및 경쟁 우위는 업계에서 필수적이며, 점점 더 많은 제조업체들이 차세대 제품에 이러한 기술을 채택하고 있습니다.사실 메커트로닉스 시스템, 컨트롤러, 온보드 계산(On-board computation), 빅 데이터, 기계 학습 및 산업 인터넷(IIoT)과 같은 여러 신기술의 통합과 발전은 선구자적인 리더들이 차세대 산업혁명 또는 4차 산업에 대해 논의하도록 이끌고 있습니다.
2. 시스템 설계 접근방법과 디지털 트윈(Digital
Twin)
제조업체들은 전통적인 설계 공정 및 관행에 관해서 자신의 가정에 도전해야 합니다. 더 이상 많은 설계 프로젝트를 규정짓는 “build
it and tweak it” 접근을 제공할 수 없습니다. 대신에 수년 동안 우주 항공 및 자동차 산업에서 설계 공정의 필수적인 부분으로 입증된 시스템 설계 접근 방식을
채택해야 합니다.
제조업체들은 형식적인 요구사항 관리와 시스템 시뮬레이션에
사용되는 고 충실도 다이나믹 모델)의 개발을
통해, 공정 초기 단계의 요구 사항에 맞춰 설계를 검증할 수 있습니다. 이 과정에서 얻은 고 충실도 모델을 일반적으로 디지털
트윈이라고 합니다.
디지털 트윈은 우주 프로그램에서 시작된 개념입니다. 이 산업에서는 차량, 탐사기 그리고 임무 수행 중인 탐사선 상의 모든
시스템에 대한 변경 사항을 시스템의 시뮬레이션을 통해 테스트하여 변경 사항이 시스템에 미치는 영향을 미리 확보합니다. 이를 통해 엔지니어는 작동 중인 시스템에 변경 사항을 적용하기 전에 원하지 않는 영향을 해결할 수 있습니다.
얼마전 디지털 트윈은
처음부터 철저하게 실제 시스템의 최종 사양을 토대로 개발되었습니다.그러나, Maplesoft의 MapleSim과
같은 강력하고 사용하기 쉬운 수학 시스템 모델링 도구 및 (엄격한 시스템 설계 프로세스의 출현으로 디지털 트윈은 설계 프로세스 전반에서 기능 검증을 위한 시뮬레이션
도구를 사용하는 것이 당연한 결과가 되었습니다.
대부분의 산업 자동화 플랫폼은 디지털 트윈의 실시간 구현을 통합하는 방법 중 하나인FMI(Functional Mock-Up) 인터페이스를 지원하여 실제 기계와 인라인(In-line)으로 실행할 수 있습니다. 이를 통해 신속한 작업 계획과 실제 시스템에서 시스템 변경이 이루어지기 전에 가상으로 테스트가 가능하게 합니다.
지난 수년 동안 다분야 시스템의 동적 모델을 만드는 데 비용이 크게 감소하였고, 이는 대부분의 기계 제조 설계 프로젝트의 예산 범위 내에 들어가게 되었습니다. 설계 프로세스 초기에 문제를 식별하고 다루는 것은 많은 비용을 절약할 수 있고, 특히 프로토 타이핑 또는 그 이상 단계의 후기 설계 요청에서 프로젝트 일정과 관련된 손실을 예방할 수 있다는 것이 여러 프로젝트에서 입증되었습니다. 따라서 도구를 위한 선행 비용에 대한 수익과 이 프로세스를 구현하는 전문 기술이 매우 신속하게 실현됩니다.
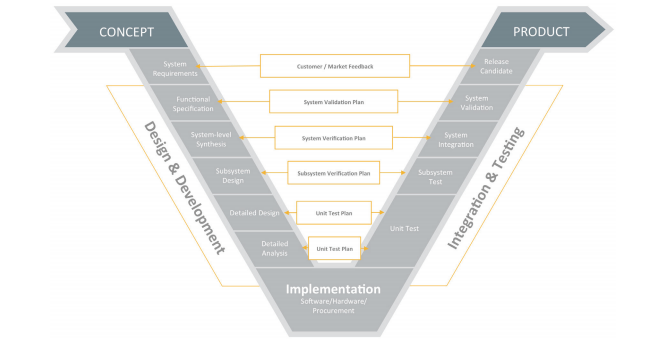
그림 1 – 시스템 설계 프로세스는 종종 프로세스의 모든 단계에서 설계를 요구 사항과 검증하는 중요성을 표현하기 위해 V 다이어그램으로 표현됩니다.
3. 가상 프로토타입(Virtual Prototype)을 뛰어넘어서
업계에서 디지털 트윈은 설계 과정을 넘어 무한한 가능성을 제시합니다. 예를 들어, 인라인 디지털 트윈은 전용 트레이닝 시뮬레이터에 대한 비용 없이도 실제 기계를 작동하는 데 필요한 기술과 확신을 가질 때까지 작업자를 가상 시스템에서 교육할 수 있게 해줍니다.
인라인(In-line) 디지털 트윈을 사용하면 학습 과정이 가속화되고 장비가 손상될 위험을 최소화할 수 있습니다. 또한, 디지털 트윈은 실제 장비와 잠재적인 문제점을 식별하는 데에도 사용할 수 있습니다.
고 충실도의 물리 모델이 실제 기계와 병렬로 실행되고, 실제 기계의
오작동 또는 잠재적인 오작동을 즉각적으로 식별하는 시나리오를 상상해 보십시오. 부품의 과도한 마모는 기계의 성능과 모델의 거동 사이의 마찰로 나타낼
수 있습니다. 이는 쉽게 노화될 수 있습니다. 기계와 같이 정확히 동일한 물리적 구조를 가진 모델은, 모델 내에서
변동 원천을 파악하고 작업자에게
기계의 수명과 진단 비용을 절감하는 지표를 제공할 수 있습니다. 한걸음 더 나아가서, 만약 이 같은 결함이 치명적이지 않다면, 생산을 늦추거나 멈추지 않고 성능 저하를 보완하기 위한 전략을 제공하기 위한 모델을 사용하는 것이 가능합니다. 이 시나리오는 최적의 제어 및 모델 예측 제어 기술의
출현과 고급 기계 학습 기능의 결합으로 가능하게 됩니다.
IIoT 기술을 통해 작업자와 원격으로 통신할 수 있는 시스템을 갖추고 있기 때문에 머지 않아 자동차 산업에서 볼 수 있는 것과 같이 기계 자율성 증가의 구현을 볼 수 있을 것입니다. 기계는 작업자와 통신할 뿐만 아니라 서로 또는 스스로 통신하게 됩니다.
임베디드 디지털 트윈은 기계의 자체 인식을 높이기 위한 기반을 제공하고, 주어진 작동 주기(Duty cycle)를 위한 성능을 최적화 하는 것을 가능하게 합니다. 또한, Non-catastrophic 결함을 진단하고 보완하며 작업자의 최소한의 입력으로 다른 기계들과의 운용을 조정할 수 있습니다.
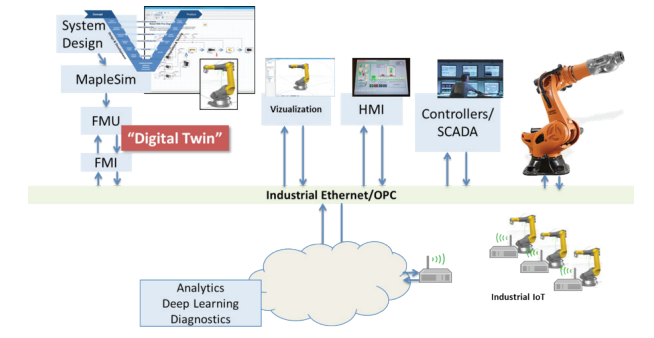
그림 2 – 디지털 트윈은 제품 개발에 대한 시스템 설계 방식을 채택한
자연스러운 결과이며 교육,인라인 진단(In-line diagnostics), 성능 최적화 그 이상을 위해 최종 제품에 쉽게 통합될
수 있습니다.
4. B & R 자동화: 디지털 트윈을 사용한 가상 커미셔닝(Virtual Commissioning)
공장 및 소프트웨어의 자동화 시스템 분야의 선두 업체인 B & R Automation은
Automation Studio 플랫폼에서 MapleSim을
사용하고 있습니다.
MapleSim을 사용하면 기계 설계자가 CAD 표현에서 직접 기계 설계의 가상 프로토 타입을 생성하고 FMU(Functional Mockup Unit)과 같은 실시간 플랫폼의 디지털 트윈으로 통합할 수 있습니다. 이러한 방법으로 가상 머신을 실제 머신과 병렬로 구성 및 테스트하여 커미셔닝 프로세스(Commissioning process)를 가속화하고, 위험부담을 줄이고 비용을 절감할 수 있습니다.
5. 혁명은 바로 지금!
제조 시스템이 설계되는 방식의 주요 변화가 일어나는 것은 의심의 여지가 없습니다. 메커트로닉스의 통합 또는 cyber-physical 기술과 데이터
관리, 기계 학습 및 통신의 발전과 함께 이미 전통적인 산업 기계 설계 프로세스에 도전하고 있습니다.
제조업체는 개발 프로세스의 핵심에서 고 충실도의 가상 프로토 타입 또는 디지털 트윈을 사용하여 종합 시스템 개발의
복잡성을 수용하는 엄격한 설계 프로세스를 시작해야 합니다. 만약 그렇지 않는다면, 제조사들은 곧 자신들이 뒤처져 있다는 것을
알게 될 것입니다.
4차 산업 혁명이 이제 시작되었습니다. 얼리어답터는 이미 4차 산업 전략의 일환으로 디지털 트윈의 힘으로
혜택을 보고 있습니다. 이러한 프로세스를 지원하는 Maplesoft 기술의 사용을
통해 기업은 쉽게 4차 산업을 구현하고 그 장점을 실현하며 경쟁에서 앞서 나갈 수 있습니다.
IoT(Internet
of Things, 사물 인터넷):
실생활에 해당하는 각종 사물에 센서와 통신기능을 내장하여 오프라인의 모든 정보를 온라인으로 넘겨 인공지능을 이용한 최적의 해법을 제시하고, 시행하게 하여 생산성을 최대한으로 올리는 도구
Mock-Up:
비행기 자동차 등의 개발 단계에서, 실제 비용을 아끼기 위해 최소한의 비용으로 실제 제품의 대략적 모습을 보고, 사전에 손보고, 검토하고, 개선까지 고려하여 최소한의 비용으로 최대한 완성품의 완성도를 높이기 위한 사전 테스트.
Digital
Twin VS Mock-Up:
디지털 트윈은 생산과 소비의 현장에서 벌어지는, 감가상각이나 돌발변수
같은 예측 불가 요인에 반응하고 그에 맞춰 신호를 보내는 반면, Mock-Up은 실물이든 가상이든 현재까지의
처음 만들어진 상태 그대로 멈춘 채 존재한다. 즉, 설계자가
특정 의도를 갖고 별도 요소를 투입하기 전엔 스스로 변화하지 않는다.
CPS(Cyber-Physical
System, 가상 물리 시스템):
IoT(사물 인터넷)과
매우 밀접한 관련이 있는 기술로 센서와 액추에이터를 갖는 물리 시스템과 이를 제어하는 컴퓨팅 요소가 결합된 차세대 네트워크 기반 분산 제어 시스템.
IoT
& CPS:
IoT이 통신 기술에 기초하여 수많은 사물들을 연동하는 기술이라면, CPS는 IoT로 구축된 환경에서 가상 공간의 컴퓨터가 네트워크를
통해서 실제 물리 시스템을 기술.
Mechatronic(기계
전자 공학):
기계와 전자의 융합기술로서, 지능형 로봇 반도체/디스플레이 제조장비 등 각종 자동화 장비 산업의 기반이 되는 기술. 요소기술로는
기계설계, 제어, 임베디드시스템 기술 등이 있으며, 한나라의 제조 산업 경쟁력을 결정짓는 핵심기술이기도 하다.
FMI(Functional
Mock-Up Interface):
복잡한 사이버 물리 시스템을 개발하기 위해 컴퓨터 시뮬레이션에 사용되는 표준화 인터페이스